Pittsburgh’s Garfield neighborhood is getting a special delivery.
A modular home, dubbed The Picket Fence, is being constructed at Structural Modular Innovations in Strattanville, in eastern Clarion County, and is expected to be transported in modules and assembled on an empty lot on North Aiken Avenue by year’s end.
“Modular building is gaining traction as a people- and planet-first solution in homebuilding, and The Picket Fence is an exhilarating milestone that will be a testament to the power and effectiveness of the modular process,” Eric Newhouse, vice president of innovation at Structural Modular Innovations and factory liaison to EcoCraft Homes, said in a statement.
The work can streamline construction practices, reduce construction time, limit embodied carbon and operational carbon emissions, and mitigate the use of non-renewable sources.
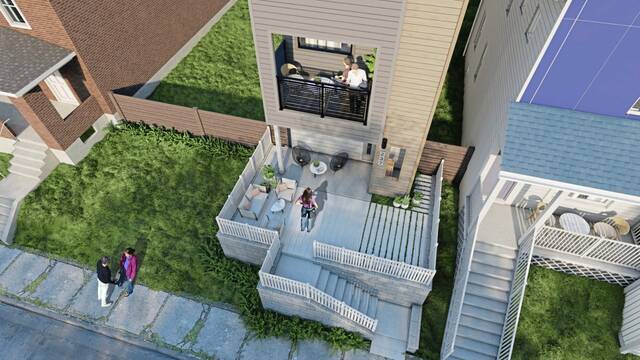
The concept came from the results of a three-phase America at Home Study. It surveyed U.S. adults, aged 25-74, from diverse backgrounds with annual household incomes of $50,000 per year or more about how they feel about and live in their homes, and what changes they’d like to see as a direct result of the covid-19 pandemic.
Those changes are reflected in The Picket Fence design, which has two for-rent units within the same structure. It’s three stories and includes a 2,007-square-foot townhome plus a 660-square-foot full studio accessory dwelling unit with an entry porch. There are three bedrooms, 2.5 bathrooms, a flex space, an entry porch, and a front-facing covered deck.
The kitchens are sized to be better equipped for cooking. The primary bedroom is a focus because survey participants said the space is for more than sleeping — it is for watching television and at times, work. The main home has a flex space on the main living level to provide a quiet place to work while providing enough space and natural light for other activities.
“The insights we gathered from the America at Home Study showed us pressing changes in how people want to live today,” said Teri Slavik-Tsuyuki, co-founder of the America at Home Study. “As a concept home, The Picket Fence will have clear and measurable data to track, allowing us to share our learnings. Experimental housing solutions are essential if we want to make a dent in America’s housing crisis.”
There is a severe shortage of housing units to keep up with the population of the nation, driving up the price of homes to levels that are not sustainable. According to John Burns Research & Consulting, there will be a need to add 1.55 million houses per year from 2020 to 2030 to catch up with the current shortage, household formation and replace aging inventory.
We have increased our forecast for housing demand for this decade from 1.55 million homes/year needed to 1.72 million homes per year needed, including manufactured homes.
3 reasons:
1 - Undersupply
2 - Household formation increases caused by work from home
3 - New Census data pic.twitter.com/AHpdhjR2XT— John Burns (@johnburnsjbrec) September 12, 2022
There is less building due to lack of construction labor and available lots. Local laws and zoning requirements don’t allow the kinds of housing that needs to be built. Lack of building materials and tougher lending conditions add to the problem. Also, more than a quarter — 27.6% — of all U.S. occupied households were one-person households, according to 2020 data by the U.S. Census Bureau.
Slavik-Tsuyuki said livability includes an integrated heart and hub of the home as a social center; front porch and outdoor livability; and personal space in the primary bedroom and spaces throughout that honor the hybrid of work/life that is here to stay.
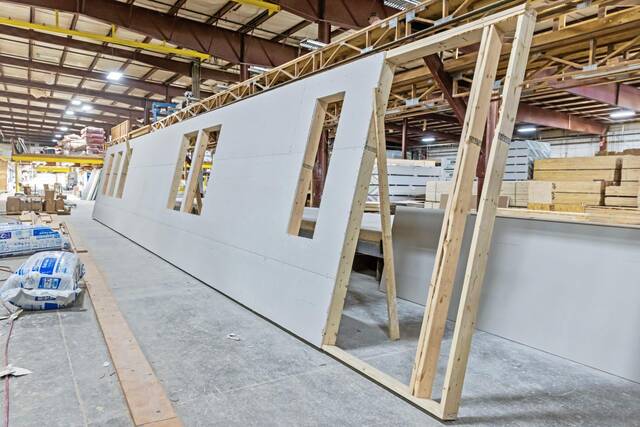
She said constructability uses a systems approach to engineer systems such as framing, plumbing, heating, ventilation, air conditioning and electrical prior to construction. There is a digital design that reduces the number of variables.
When it comes to sustainability, this process can reduce carbon emissions by 70% and generate 90% less construction waste by selecting alternative raw materials with lower environmental impacts.
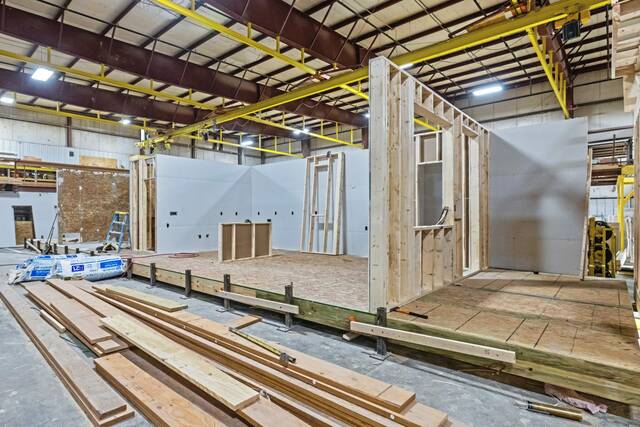
Building offsite, they can deliver higher quality homes at a faster pace, according to Ryan White, director of design for DAHLIN | Architecture | Planning | Interiors in Irvine, Calif. White said when building in a factory, the team pays close attention to make the most of every input through the design, engineering and production details. This ensures there is minimal cutting and material thrown aside. The excess can be repurposed — as opposed to a typical site-built home under construction where there is a large dumpster overflowing with leftover materials.
Featured Local Businesses
Dennis Steigerwalt of Oakmont, president of Pittsburgh-based Housing Innovation Alliance, said the off-site building process is beneficial because there are no weather delays and more quality control. He said Pittsburgh is the perfect place to do this and said the hope is it will have a ripple effect that extends beyond Pittsburgh.
“There is a culture and a commitment — perhaps maybe best described as grit — to rally around complex programs to do better, be better,” he said. “Pittsburgh is a city that is constantly evolving to solve for what the world needs – rising from its industrial roots.”
Pittsburgh is made up of 90 neighborhoods. What excites the team about this one is a commitment from leadership at the Bloomfield-Garfield Corporation for a vibrant and thriving neighborhood, Steigerwalt said.
“We also appreciate their proactive scattered-site community-led development to bring vacant spaces back to life and add value for the community,” Steigerwalt said. “This area was a farmland through the 1800s and today it is still home to community gardens and farms.”
He said there is clear evidence of neighborhood and city pride and it’s a great place to celebrate Pittsburgh’s history and its future, creating opportunity for a diverse range of backgrounds and income levels to call the neighborhood home.
He said Garfield’s location between UPMC Children’s Hospital of Pittsburgh in Lawrenceville and the East End tech hub with Google, Duolingo and Philips are benefits, as well as being close to area universities. It also has some “great views.”
They paid $8,000 for the land in 2021, but this does not take into consideration the legal fees, transfers taxes, title insurance, and other closing expenses, Steigerwalt said. There is substantial planning and site-related expenses when it comes to building on these types of infill lots that make cost-effective development challenging, he said.
He said The Picket Fence rental home is being designed for those he calls “trailblazers,” a millennial demographic who seek a modern and sustainable living space that suits their active urban lifestyle.
The rental amount for The Picket Fence will be determined closer to completion.
A second modular home is planned for Lawrenceville and it will be called The 412. Factory construction is expected to start in December or January.
JoAnne Klimovich Harrop is a Tribune-Review staff writer. You can contact JoAnne by email at jharrop@triblive.com or via Twitter .