Harry Vine Homes, a modern modular home building company, prefabricates houses in a climate-controlled warehouse before transporting them to a specific address — a practice that can be a viable solution to the housing shortage.
According to Habitat for Humanity of Greater Pittsburgh, there is a severe shortage of both rental and homeownership opportunities in the city. It is estimated that there is a need for roughly 15,000 affordable homes.
The lack of decent, affordable homes has forced tens of thousands of local, limited-income families to pay well over 30% of their monthly income on housing. Half of those earning 30-80% of the Area Median Income are cost-burdened by their housing, meaning over 30% of their income is spent on housing, according to Habit for Humanity of Greater Pittsburgh.
“These builds provide tremendous affordable opportunity to infill otherwise vacant or underutilized parcels of land,” said Scott Rykala, real estate and development program manager for Uptown Partners of Pittsburgh.
Modular homes can provide a means to bridge the gap found within the housing market by providing sustainable and affordable opportunities for homeownership through abundant, affordable and sustainable housing, Rykala said.
He said when speaking specifically about vacant property, the floor plans of some modular homes take up very little space within a designated parcel.
“With that, those builds may allow a smaller parcel to be activated, allowing individuals or families to call the space their home,” Rykala said. “Additionally, modular builds are usually more energy efficient by way of lighting, heating and other utilities because of the size of the build all at a fraction of the cost.”
Rykala has had conversations about this style of residence with the founder of Harry Vine Homes, Bob Hartle, about developing desperately needed attainable housing in and around the city.
“We are thrilled about the potential to partner with local groups who can use their resources to make homes affordable to the end user,” said Hartle.. “On our end, the costs and process are the same whether we sell to a community-focused organization or private citizen. Due to the modest footprint and process efficiencies we have developed, we’re able to pass added value on the customer, making our homes more attainable compared to other new construction options that exist.”
Hartle said the homes are designed to provide modern living in an efficient space. He uses a a streamlined process to where the residences can become a fully finished home in six weeks. Just like stick-built homes, which are built on-site, these houses also must pass inspection, Hartle said.
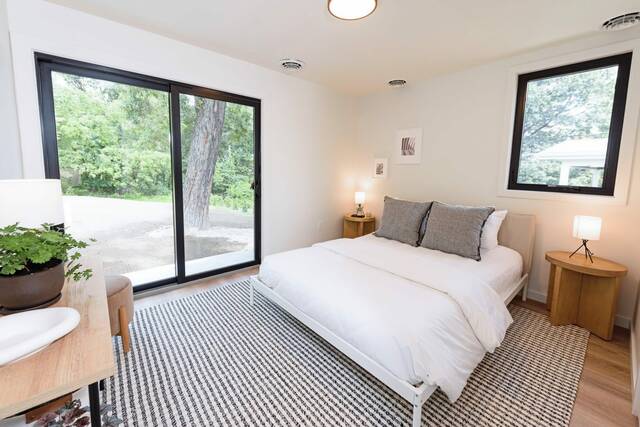
Hartle, an Allegheny Township native who lives in Stanton Heights, has been investing in real estate and doing home remodels for more than a decade. He has bought, renovated and flipped dozens of modest-sized homes, which inspired his interest in modular home building.
“Buyers for these homes came from many different segments of the population,” Hartle said. “I noticed how many people wanted — or needed — a high quality, low maintenance living space they could call their own, and afford at the same time.”
Prefabricated homes allow home buyers to get more for their budget through better design and controlled building processes, he said.
“We strive to redefine what it means to build a home in the 21st century,” Hartle said.
Harry Vine Homes constructs the entire house in a climate-controlled factory in Lawrenceville and then coordinates delivery with a transportation company and on-site builder.
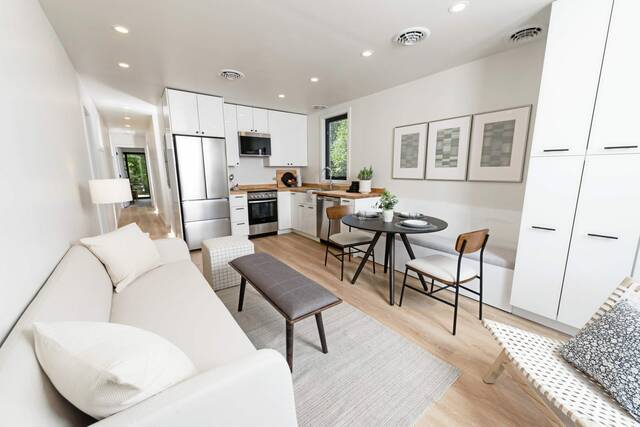
The homes have metal roofs, vinyl plank flooring, Anderson windows, 42-inch cabinets, full-size kitchens and highly efficient furnace and air conditioning systems. The homes are powered by electricity — there are no gas appliances or heating.
The two homes recently installed in Millvale are both 600 square feet, have two bedrooms and one bathroom and started at $150,000 each.
Featured Local Businesses
Additional costs include permitting, site work, utility tap-ins, transportation, crane rental and taxes, Hartle said. Site conditions determine the cost for site work and utility tap-ins, so builder costs will vary from project to project, Hartle said.
Once a house is set on the permanent foundation, it is attached in the same manner a site-built home would be. The on-site builder takes care of utility connections and finish work.
Harry Vine Homes is the only Pennsylvania Department of Community and Economic Development-approved modular home manufacturer in the city of Pittsburgh.
Hartle said some people might think of these homes as mobile homes.
“This is obviously not the case, with modular homes being set on a permanent foundation,” Hartle said. “That is simply a lack of awareness, which will subside as off-site construction becomes more prevalent.”
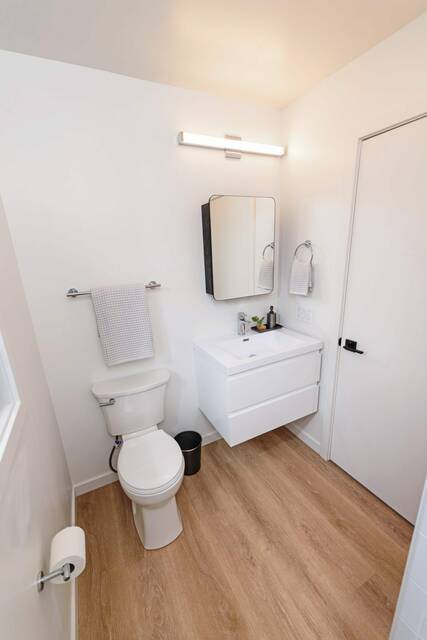
He said these homes are perfect for customers who want to build an adjacent home for a family member or want a separate space for company. He said seniors wanting to downsize or people looking for a starter home have inquired about these homes, and they can be utilized as an Airbnb.
“Pittsburgh has so many narrow, deep lots so this works perfectly,” Hartle said. “They add to the aesthetic of the neighborhood.”
Elizabeth Sublette became enthralled by prefabricated homes when living in Oregon, primarily due to size and efficiency as well as the environmental benefits, she said. She purchased one of the Harry Vine Homes on Anderson Avenue in Coraopolis.
“What I like most is the modern style, the functional layout with ample storage and the exceptional finishes,” Sublette said. “It’s perfect for my minimalist way of living.”
JoAnne Klimovich Harrop is a TribLive reporter covering the region’s diverse culinary scene and unique homes. She writes features about interesting people and a weekly column about things to do in Pittsburgh. The Edward R. Murrow award-winning journalist began her career as a sports reporter. She has been with the Trib for 26 years and is the author of “A Daughter’s Promise.” She can be reached at jharrop@triblive.com.